Depending on the configuration of anchor rod, some or all of the following procedures may be required. An anchor rod’s ASTM grade may also have additional processes involved with the manufacturing of the final product. Below are the required steps in producing the specified anchor rod configurations in question.
Cutting
Anchor rods start out as steel round bar, usually in 20’ to 40’ lengths. Before anything can be done, the round bar needs to be cut to the desired length. There are two ways the steel would be cut, either by shearing the material or saw cutting. The diameter of the steel, the number of parts being cut, or the ASTM grade of steel, would be the deciding factor as to whether the parts are sheared to length or cut using a band saw. If sheared, a blade chops the steel similar to a guillotine and is a much more efficient method compared to band saws, which use blades with teeth to cut through the steel. The advantage to saw cutting is that there is no limitation as to what can be cut, whereas the shearing method may be limited to smaller diameters and lengths.
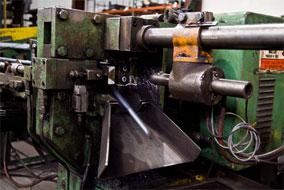
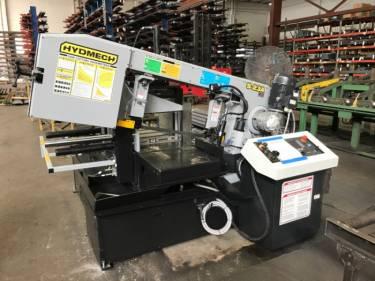
Chamfering
After the anchor rod has been cut to length, the ends are chamfered. This creates a slight bevel where the first thread would be. The reason for this is because often times when steel is cut to length, it leaves a sharp edge or burr on the edge, which after threading can make it difficult to assemble a nut. By creating a chamfer, you are ensuring that the nuts will thread on to the rod smoothly and have no issues during installation. This process is extremely important when fabricating high strength anchor rods or rods that will be hot-dip galvanized.
Threading
Regardless of the configuration, all anchor rods will be threaded on at least one end, but normally they would have threads on each end or fully threaded. One of the threaded ends of the rod will project from the concrete to anchor down structural steel columns, light poles, traffic signals, sign structures, and industrial equipment to the foundation. The threads are commonly created with one of two types of threading processes. Cut threading, a process where the steel is cut away from the round bar to form the thread is common for small quantities of anchor bolts, large diameters, and high strength anchor rods. Roll threading forms the threads through an extrusion process in which threading dies displace the steel to form the thread and is a more efficient method of threading.
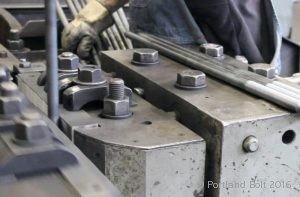
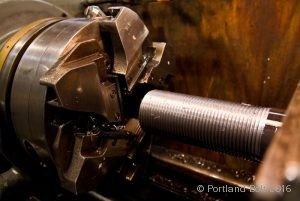
Heading
If the anchor rod being used possesses a forged head on the embedded end, the unthreaded end of the round bar is heated via an induction process and placed into an upsetter where a plunger compresses the heated steel to form the head of the anchor rod. This headed end is embedded in the foundation with the threaded end projecting from the concrete. The headed end can be forged into a hex head, heavy hex head or square head. The purpose of the forged head on the embedded end is to create pull-out resistance.
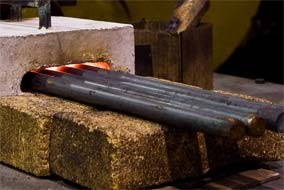
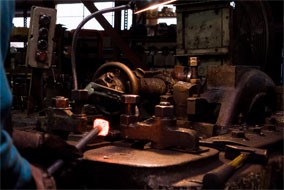
Welding
Welding is a process in which pieces of steel are bonded together by heating the components and combining a filler material of molten metal. Anchor rods are commonly welded for multiple reasons and in different ways. The most common welded configurations are a welded nut at the bottom of a rod, a nut welded to an anchor plate, and a plate sandwiched between two nuts and welded. It is important to consider the grade of steel and nuts before welding since there are many grades of steel and nuts which are technically not weldable. F1554 Grade 36 is always weldable and F1554 Grade 55 has a supplemental requirement for weldability, which is common, however welding to F1554 Grade 105 should be questioned since this grade is heat treated and may be unpredictably altered by applying high heat. This applies to any grade that gains its strength through a heat treating process. Welding can be avoided by sandwiching an anchor plate between two nuts and/or staking threads one a nuts is assembled to prevent it from backing off.
Swedging
Anchor rods can also be swedged, which consists of pressing large indentations or dimples into the surface of the embedded end that allows concrete, grout, or epoxy to fill into the indentations. The concrete, grout, or epoxy forms around the indentations and this creates pullout resistance instead of a welded nut or forged head. Swedged anchor rods are often used in bridge bearing assemblies.
Plate Fabrication
Anchor plates are typically square or round and are used on the embedded end of the anchor rod. The purpose of an anchor plate is to provide pull-out resistance for the anchor bolt. To secure the anchor plate, they can be assembled in-between two hex nuts, welded, or both. Plates can also be used for the projecting end of the rod as a large plate washer. Another type of plate used with anchor rods is a template, which houses multiple anchor rods to keep them in place during installation. This helps to ensure that the rods will be in line with the base plate bolt circle of the pole that they are holding down. Square anchor plates are sheared and punched from flat bar. Round plate washers as well as templates are normally laser-cut or plasma burnt. Anchor plates are normally manufactured to ASTM A36 or A572 Grade 50, however since templates are normally temporary, they are typically A36.
Grade Identification
Many grades of anchor rods require a permanent grade symbol and manufacturer’s identifier on the end of the rod that projects from the ground. An exception is ASTM F1554, which requires color coding (blue, yellow, or red). If a permanent grade identifier and/or manufacturer’s identifier is requested under the ASTM F1554 supplemental requirement, they would be stamped on the projecting end as well as color coded. A hydraulic stamping machine applies these permanent identifiers after the rods have been cut and chamfered. If the anchor rods are galvanized, the end would be stamped after galvanizing so that the grade symbol is legible.
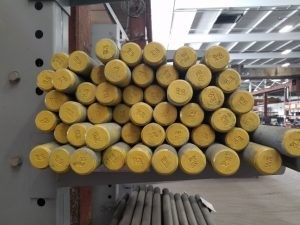
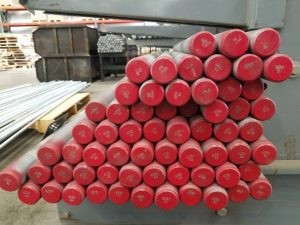
Galvanizing
Due to anchor rods often being installed outdoors and exposed to the elements, it is common for anchor rods to be hot-dip galvanized per ASTM F2329 or ASTM A153 Class C. Galvanizing is a process in which zinc is applied to steel products to protect against corrosion. It is critical that the anchor rods be galvanized in a system designed specifically for threaded fasteners. The process of hot-dip galvanizing anchor rods does not rest solely on the dipping process, but also in the preparation and cleaning processes. It is also important that galvanized anchor rods be inspected to make sure that the threads are free of excess zinc so that they will accept a nut.
Preparation and Cleaning
During the manufacturing process, threaded rods will often collect organic material such as cutting oil, which needs to be removed. To do this, the rods need to be submerged in a caustic soda solution and then rinsed in water. The next step is to remove the hot rolled scale from the surface of the round bar and etch the surface of the steel. To do this, the rods need to be submerged in sulfuric acid and then rinsed with water. The last step in preparing the rods to be hot-dip galvanized is to submerge the rods in flux, which is a chemical that helps facilitate the reaction of the zinc to the steel.
Hot-Dip Galvanizing
The coating process involves completely immersing the rods in a tank containing 840°F molten zinc. The anchor rods will remain in the tank until the zinc has metallurgically bonded to the steel. Depending on the diameter, steel grade, as well as a number of other factors, the amount of time that the rods will need to remain in the zinc can vary. A crane lifts the rods while the zinc is still liquid and a high-speed spinner functions like a centrifuge to remove the excess zinc from the threads. This produces the highest quality threads and trouble-free nut fit.
Inspection
Once the rods have been taken removed from the galvanizing tank and the threads have been cleaned, it is critical that there be a system set in place to thoroughly inspect the threads as well as a method for cleaning any excess zinc that may have built up. This is to ensure that all of the threaded rods are able to accept a nut without the nut jamming. Inspection of the finished, galvanized rod is critical for a good nut fit. Note that chasing threads (rethreading after galvanizing) to clean excess zinc from the threads is not permissible under ASTM galvanizing standards.